Le quattro sfide della nuova manifattura
L’industria manifatturiera richiede nuovi modelli innovativi e più evoluti di filiere industriali. Ha necessità di catene di fornitura ridisegnate radicalmente in funzione della nuova sfida non solo delle due transizioni, energetica e digitale.
L’industria manifatturiera ha di fronte almeno altre quattro grandi scommesse che richiedono nuove filiere ripensate secondo la logica della riconfigurazione delle catene del valore. Nuove catene di fornitura che vanno rivisitate e sostenute per rispondere rapidamente ai cambiamenti improvvisi della domanda e per adattarsi a interruzioni impreviste. Ma c’è un ostacolo ancora su questo percorso: le filiere non sono ancora così connesse e digitalizzate come i nuovi paradigmi richiederebbero in una logica di ecosistema ampio e organico: «Non si può più fare da soli, così come non si può più essere né sostenibili né sconnessi digitalmente dalla propria catena di valore. Le capacità tecnologiche devono essere di filiera, e questo comporta un costante lavoro di assessment digitale e di mappatura dei limiti e delle potenzialità». L’alta specializzazione è il collante delle filiere, gruppi di imprese che si ritrovano tutte intorno a un prodotto, seguono uno stesso metodo di lavoro, hanno una relazione spesso anche solo informale, ma con una grande capacità specialistica e di flessibilità che consentono di essere molto aderenti alle necessità del cliente. C’è un altro fronte che va tenuto in considerazione: l’alta specializzazione sta creando anche un nuovo fenomeno di “collaborazione”, imprese non più solo legate a una filiera di un singolo settore industriale. Ma aziende diventate anelli anche di filiere di settori industriali diversi e trasversali. Emergono così imprese inserite e protagoniste di veri network industriali connessi, e anche questa è una novità nel panorama delle nuove filiere dell’industria manifatturiera.
Ecco anche perché ora le nuove supply chain impongono che tutte gli anelli della filiera avanzino alla stessa velocità, con lo stesso metodo, utilizzino lo stesso standard produttivo e che l’intera filiera sia sostenibile. «Nessuna impresa deve restare indietro, solo perché c’è un’azienda che va troppo veloce sulla strada della digitalizzazione».
C’è però un secondo limite con cui fare i conti nell’ottica di ridisegnare le catene del valore. Le piccole imprese, quasi sempre eccellenze nella fornitura di componenti alle imprese e alle industrie a capo della stessa filiera, sono anche le aziende più in ritardo sul fronte della transizione digitale.
Il ritardo delle Pmi: troppo passive sul digitale
Il dato più confortante indica che oggi, in particolare le medio-grandi aziende hanno realizzato un livello digital nell’organizzazione, nei processi industriali e nei prodotti sostanzialmente al pari delle imprese europee. Ma sono le più piccole imprese a dover ancora affrontare questo “salto quantico”: la nuova ricerca dell’Osservatorio Innovazione digitale nelle Pmi del Politecnico di Milano, ha infatti sancito che il 47% delle piccole e medie imprese italiane sono ancora “troppo timide” e “passive” sulla strada della digitalizzazione, con un 7% addirittura di “irriducibili”, quasi costretti a innovare e che vedono ancora il passaggio digitale in funzione del costo e non invece del valore che crea.
Il lato positivo della ricerca, dall’altra parte, mostra invece un 53% di Pmi che comunque considera la transizione digitale una leva di competitività, e quindi da perseguire con convinzione. Resta però un punto oscuro sull’intero approccio: se prima della pandemia meno di due imprese su dieci (il 14%) si avvicinava al digitale con un approccio strategico, ora quasi sei su dieci investe nel digitale per raggiungere specifici scopi strategici, ma per ancora tre aziende fra quest’ultime si tratta di “un approccio reattivo, come investimento sollecitato da stimoli esterni, per esempio la pandemia”.
Dentro alle nuove filiere non possono più esserci aziende che “viaggiano” a velocità differenti rispetto alle altre, che sono disegnate in modo diverso, con metodo di lavoro differente. Per questo l’attenzione sulle nuove filiere non può prescindere dai punti cardine di questo percorso e tutti racchiusi nel nuovo concetto alla base dell’industria manifatturiera del futuro: Innovability, l’innovazione che si accompagna necessariamente con la sostenibilità.
Ed ecco allora quali sono le quattro le sfide da affrontare, dove ciascuna rappresenta anche i quattro pilastri del nuovo sistema di produzione manifatturiero che verrà e dai quali, come è stato spiegato dal presidente uscente di CFI, Luca Manuelli, dal presidente del DIH Lombardia, Gianluigi Viscardi, e da Tullio Tolio, docente al Politecnico di Milano, nella presentazione della nuova roadmap del Cluster Fabbrica Intelligente, «arrivano dalla base, dalle imprese e dall’ecosistema industriale le sollecitazioni e gli spunti più importanti dei cambiamenti che si dovranno affrontare».
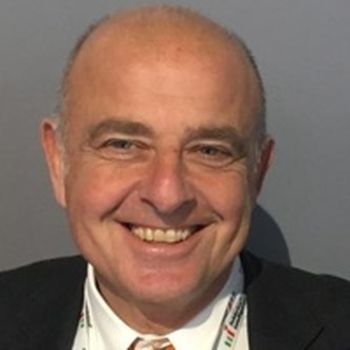
Presidente uscente di Cluster Fabbrica Intelligente
La roadmap messa a punto è molto dettagliata, disegnata mutuando lo schema algebrico della matrice in cui sugli assi orizzontali figurano i temi sfidanti per la manifattura del futuro, mentre in verticale sono indicate le piattaforme abilitanti e i processi produttivi innovativi di queste trasformazioni, altro concetto in cui l’Europa è decisamente in ritardo rispetto agli Usa o alla Cina.
La roadmap della Fabbrica Intelligente per le filiere
Non è un caso, quindi, se la roadmap del Cluster Fabbrica Intelligente indica come prima trasformazione dei modelli di filiera produttivi quella indotta da una mobilità elettrica sempre più diffusa, un cambiamento che ha già iniziato a ridisegnare l’intera filiera dell’automotive, sia sul lato della produzione sia delle relazioni fra produttori e fornitori di componentistica a causa della svolta tecnologica. Ma la trasformazione coinvolge le filiere dell’intero sistema delle infrastrutture per il caricamento dell’auto elettrica, le smart grid per il dialogo con le auto connesse e tutto il sistema industriale per la produzione delle batterie e del loro riuso, del recupero e del loro riciclo.
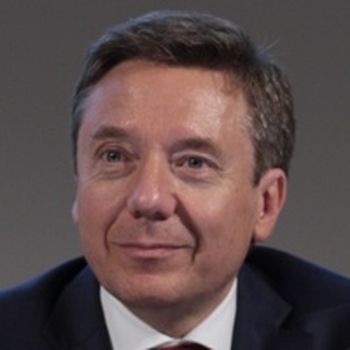
Docente Politecnico di Milano
Seconda sfida: la svolta ecologica e energetica sta decisamente imponendo nuovi modelli culturali e direttamente nuovi paradigmi di consumo, di comportamento, di stili di vita. In questo senso i trend segnalati dalla roadmap sono molto chiari: crescono sempre più le figure di consumatore-designer (è il cliente che progetta il proprio prodotto), cresce anche il consumatore eco-frendly rispettoso dell’ambiente nei suoi consumi. Qui la scommessa per il manifatturiero sarà prevalentemente concentrata su filiere e sistemi di produzione in grado di aumentare la capacità di “personalizzare” sempre più i prodotti finali. Per le imprese della stessa catena di fornitura tutto questo significa adottare sistemi di configurazione dei prodotti in grado di interfacciarsi con sistemi produttivi avanzati, a monte e a valle della catena., fino ad arrivare a una nuova “customer experience” in negozio e online attraverso le nuove tecnologie come i sistemi di visione, di realtà virtuale e aumentata.
Una filiera a impronta circolare
Terza sollecitazione: la transizione ecologica pone la sfida forse più radicale e culturalmente importante per una filiera di fornitura: tutta la catena deve trasformare i processi produttivi in un’ottica e secondo i paradigmi dell’economia circolare. Non più prodotti che vanno al cliente e lì restano, ma prodotti che tornano indietro all’azienda.
Significa estendere la vita utile di un prodotto, prevederne il riciclo di diversi tipi di rifiuti, progettare prodotto secondo le regole europee dell’eco-design. Tutto questo avrà un impatto diretto sulle strategie di produzione e solleciterà anche la nascita di nuove imprese con una nuova capacità di progettare e di creare – innovando e con flessibilità - nuovi prodotti nel momento in cui emergeranno bisogno fino ad allora sconosciuti e imprevisti (l’emergenza sanitaria ha dato un’ampia prova di questa capacità con le tante riconfigurazioni industriali messe a terra sulla spinta dei nuovi bisogni di mercato emersi con la pandemia).
Da modello di produzione lineare si passa a una modello di produzione circolare perché che deve comprendere la capacità di misurare, di monitorare il livello reale di sostenibilità ambientale e sociale.
Il passaggio tecnologico e le persone come registi
Ultima sfida sul tavolo per il manifatturiero è tutta di tipo tecnologico: la necessità di introdurre nella fabbrica del futuro (già oggi in attività) sistemi digitali trasversali e diffusi ogni livello dell’organizzazione aziendale. È la nuova gestione della conoscenza e della competenza attraverso l’adozione sempre più massiccia di sistemi di Internet of Things (IoT) e di Intelligenza artificiale (AI). Digitale diffuso e al massimo livello, ma anche – rimarca la roadmap – con la massima importante integrazione con le persone. «Il manifatturiero è certamente la palestra della nuova digitalizzazione, ma la transizione digitale non è solo un passaggio tecnologico. Sono sempre le persone che adeguano l’organizzazione, che modellano le aziende intorno a se stesse. In questo occorre come indispensabile un sostegno continuo in termini di formazione continua e di aggiornamento delle competenze perché il digitale non è solo questione di software».
È quest’ultima dimensione, però, la digitalizzazione o la maturità digitale raggiunta dalle piccole imprese, il passaggio che sta dando maggiori problemi sulla strada della ridefinizione delle nuove filiere industriali. Le nuove catene di fornitura richiedono un forte passaggio d’innovazione: l’introduzione in ogni processo e funzione aziendale di soluzioni di connessione per condividere non solo informazioni, ma anche sensazioni e azioni. Prevedere la possibilità di utilizzare sensori e attuatori intelligenti di nuova generazione, per sviluppare e riprodurre il senso di presenza a distanza, ma anche – ed è il nuovo obiettivo della digitalizzazione – facilitare o garantire anche azioni e interventi da remoto.
Non è più solo una questione legata al fatto che in due anni il mondo è cambiato. E la manifattura si è trovata di fronte a due emergenze come il rischio dell’interruzione di catene di fornitura troppo lunghe e globalizzate per supply chain più corte e più “locali”. O come ora, con la guerra in Ucraina che ha prodotto un ulteriore rincaro dei costi energetici, di fronte al pericolo una interruzione delle materie prime e dei componenti essenziali per molti settori del manufacturing.
Le imprese capaci di creare una filiera integrata
Una nuova scommessa va aggiunta per le filiere del futuro: le nuove filiere saranno efficaci solo se ogni anello sarà in grado di connettersi e integrarsi perfettamente con tutta la filiera a cui appartiene, dove ogni anello di questa catena del valore possa parlare e capirsi perfettamente non solo con chi gli sta davanti o che viene subito dopo, ma possa interagire e comprendersi con ogni singolo soggetto, fin dal primo soggetto della catena all’ultimo anello. Questo perché parlano la stessa lingua, adottano lo stesso modello, si misurano con gli stessi standard e utilizzano le stesse metriche.
E gran parte dell’efficacia di queste misure fanno capo «al senso di responsabilità» dell’industria capofiliera, l’impresa attorno alla quale si è costruita e organizzata la catena di fornitura. E che continuano a mantenere la stessa grande responsabilità sulla visione di filiera. Una chiamata in causa che il Cluster Fabbrica Intelligente ha risposto mettendo a disposizione al momento sei Lighthouse (Impese Faro) – l’avanguardia della manifattura italiana avanzata, e cioè stabilimenti industriali capaci di “dimostrare” alle aziende più piccole l’efficacia “pratica” delle nuove tecnologie (i sei Lighthuse sono Ansaldo Energia, Tenova Ori-Martin, Hitachi Rail, Abb Italia e, più recentemente, Hsd e Opificio Digitale- Wärtsilä Italia).
E nell’ottica del supporto alle piccole aziende della propria catena si sono sviluppate iniziative di filiera e di Open Innovation collegate ai Lighthouse Plant che hanno permesso di coinvolgere in maniera organica fornitori tradizioni e “innovativi” delle loro filiere. Nell’ecosistema del Cluster, inoltre, sono entrati anche cinque Pathfinder (Sap Italia, Deloitte Italia, Cisco Italia, EY e Siemens Industry Software), partner tecnologici in grado di immaginare il futuro e le traiettorie delle tecnologie di cui si occupano, aiutando la community del cluster a prendere la giusta direzione sia nell’attività di roadmapping che nel supporto all’implementazione delle Fabbriche Faro.
Un progetto nato nel 2016 con l’allora Piano Calenda, il programma di trasformazione dell’industria in industria 4.0, sul modello tedesco. Ideatore e primo progettista è stato Gianlugi Viscardi, patron di Cosberg e oggi presidente del Digital Innovation Hub Lombardia.
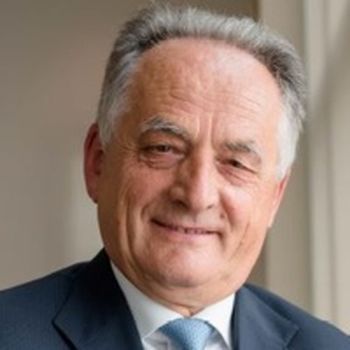
Presidente del Digital Innovation Hub Lombardia e patron di Cosberg
«Indirizzare le imprese verso percorsi di trasformazione digitale è decisivo in questo momento - spiega Viscardi -, così come strutture al pari del MADE è quello di trovare le competenze necessarie per attivare in modo concreto le attività progettuali. L’ecosistema, in senso lato, rappresenta la sintesi della filiera. All’interno di una filiera, la volontà e la capacità di poter condividere dati tra i partner - spiega Viscardi - è un elemento che aumenta il livello di collaborazione e indirettamente di fiducia tra i differenti attori. Grazie alla condivisione delle informazioni, in logica di partnership, gli attori della filiera imparano reciprocamente, creando valore. La tecnologia gioca un ruolo determinante nella trasformazione digitale e nella data economy - sottolinea il leader di DIH Lombardia-, ma sono da tempo fermamente convinto che, anche in questo “mondo nuovo”, ancora una volta sarà il capitale umano che determinerà la differenza. Il filone della nostra ricerca, che ha investigato i modelli organizzativi adottati nella trasformazione digitale, evidenzia il ruolo che sempre di più le competenze - declinate anche in nuove figure professionali – giocano all’interno delle organizzazioni. Accanto alle competenze, la condivisione della conoscenza, sia all’interno dell’azienda che all’esterno, rappresenta un fattore competitivo».
- Filiere da ridisegnare, la manifattura chiede imprese connesse, digitali e sostenibili
- Le quattro sfide della nuova manifattura
- Il ritardo delle Pmi: troppo passive sul digitale
- La roadmap della Fabbrica Intelligente per le filiere
- Una filiera a impronta circolare
- Il passaggio tecnologico e le persone come registi
- Le imprese capaci di creare una filiera integrata